This article was published in the June 2021 issue of Pet Food Processing. Read it and other articles from this issue in our June digital edition.
With pet ownership at an all-time high, the demand for innovative pet food products continues to grow. In response, pet food manufacturers are closely watching food industry trends to forecast the future demands of pet food customers who are looking for high-quality products combining nutrition and other health-oriented properties, according to Dave Carney, petfood market segment leader, Bühler, Lake Bluff, Ill.
“Pets are valued members of the family, and feeding them a minimally processed, whole food, human-grade diet is increasingly important to people and their pets,” said Carmen Velasquez, vice president of marketing, The Honest Kitchen, San Diego, Calif.
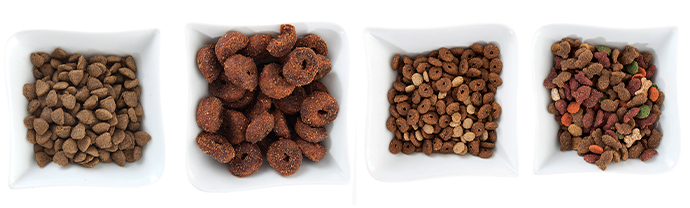
Such a mindset is producing pet food trends that mimic those in human food including the use of more high-end ingredients like fresh meats. Previously limited to mainly semi-moist or moist types of pet food, interest is spreading to the dry pet food products known as kibble.
These products look to meet the varied needs of pets with formulas for different life stages including young, adult and senior animals, small and large breeds, and active and overweight pets. Increased demand for pet foods free of common food allergens such as soy, wheat and corn find producers looking to the natural diet of wild animals with formulations including novel and sustainable proteins, vegetables, and good sources of fiber.
The production of kibble employs a process of extrusion followed by baking and drying and the option of enrobing the product in mixtures of fats, flavors, vitamins and minerals before packaging. Processors can choose from cold forming extruders, pellet mills and cookers to extrude and portion materials before drying, according to Jeff Zeak, national development manager, bakery, Reiser, Canton, Mass.
“It’s about having a modular kitchen that can produce many different products while maximizing the operational efficiency,” explained Andy Hollister, Wenger Manufacturing, Inc.
Evolutions in baking and dehydration drying machinery offer hybrid oven dryers in combinations of convection impingement technology (variable heat and air velocity), humidity control (injecting steam), and radio or microwave technology (heating, cooking and drying from the inside out).
Freeze-drying is another method for drying kibble to a lower finished product moisture content.
Evolving processes
As calls for baked kibble continue to grow, Reading Bakery Systems, Robesonia, Pa., is finding more customers in search of ways to reduce dollars per pounds. For many, the answer is found in automation, sizing the feed system, building the dryer accordingly to match the oven, and allowing customers to run bigger systems with fewer employees while achieving a more consistent product.
To improve kibble product consistency and throughput efficiency, Zeak recommends pre-blending dry ingredients as well as pre-mixing dry with wet ingredients and pre-heating mixtures to help processors improve ingredient dispersion, solubility and hydration. Reiser recommends a preconditioner mixer blender for the delivery of homogenous product mixture to the extrusion process, whether in the form of a pellet mill, cooker or a Vemag-brand cold forming extrusion machine for processing.
Running in the 5,000 to 6,000 lbs-per-hour range, Reading Bakery System’s standard baked lines fall in line with standard cookie systems. With very little effort, the oven can be sized to bake 20,000 lbs per hour, which will match the typical high pressure extruder’s throughput, said Sam Pallottini, director, cookie, crackers and pet food sales, Reading Bakery Systems.
“The preference for baked is growing in popularity because the baking process does not destroy the vitamins and proteins, helping to retain a product’s nutritional value,” Pallottini said.
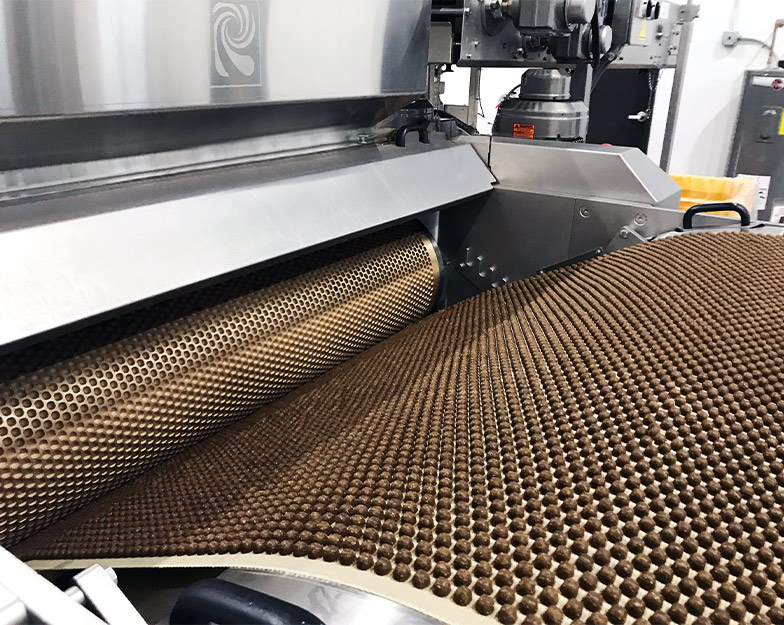
Improvements in drying technology can also reduce energy consumption, increase production throughput rate, reduce yield loss by not over-drying the product, and improve product consistency and quality by not under-drying the product and drying all the product consistently. When feed is overdried, too much water evaporates, which then must be replaced with raw ingredients – resulting in dramatic product losses over time.
Moisture Pro, a Bühler Insights tool, can capture a reading every second, helping to reduce time-based moisture deviation. As an inline moisture sensor takes a reading, a written algorithm can help control temperature settings to consistently achieve the desired output, ensuring precise moisture content is achieved along with the safety of the product. Through small, immediate adjustments, processors can continuously monitor and control the moisture content of a product exiting the dryer, leading to production gains.
New considerations
The ability to make consistent and accurate assessments is growing in importance as pet food becomes more premium. The premiumization of sustainable pet foods includes ingredients enabling a label to claim meat or fresh meat, including fresh or frozen deboned meats or innards from beef, pigs, lamb, poultry and venison, something that is driving a lot of research into the use of real meat or meat by-products, Carney shared. Alternative and unexpected protein innovations, such as alligator, duck and rabbit, are also generating interest among processors.
“Manufacturers are interested in processing the highest quantities possible in a variety of forms such as minced meats, processed meats and meat slurries,” Carney said.
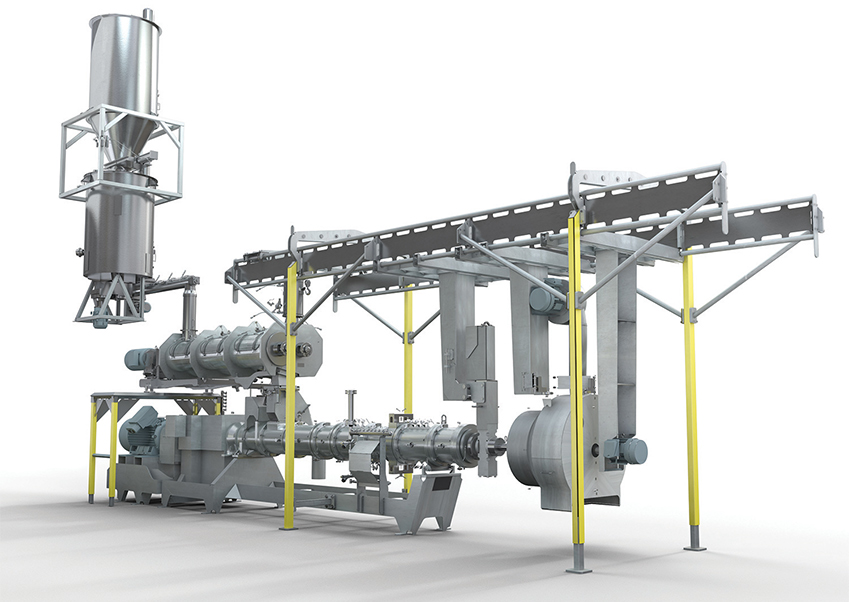
On the flip side, there is a growing call for the inclusion of plant-based ingredients and demonstration of sustainability. These on-trend products embrace ingredient transparency, featuring alternative, non-animal protein sources and low-impact processing techniques. Such innovations include the use of legumes, pulses, marine algae and insects, a sustainable food source combining high palatability and digestibility.
When fielding demand for grain-free diets containing fresh meat and fish, Clextral cautions the addition of fresh meat to kibble processing will necessitate modifications to achieve the correct moisture and texture, making testing important, according to Sylvie Brunel, process and products development manager, Clextral, Firminy, France.
The combination of high temperature and high pressure produces foods that are highly digestible and free of pathogens, she continued. Applying a continuous process in a closed system, extrusion cooking enables precise control of all production parameters from ingredient feed, through starch gelatinization via mixing, heat and pressure, and kibble forming.
In some cases, continuous process cooker extruders may have the ability to produce greater product throughput as compared to cold forming extruders used in a batch process. Cold forming extruders can offer greater flexibility of use through the application of different forming attachments for the front of the machine and can have quicker and easier product changeover characteristics as compared to a cooker extruder, Zeak said.
Looking to provide pets with a minimally processed, whole-food, human-grade diet, The Honest Kitchen sought to create a dry food that meets the company’s nutritional values. Its small-batch Whole Food Clusters combine cold pressing with dehydrating and slow-roasting to preserve the overall ingredient integrity and create a more nutritionally dense and palatable product.
Building partnerships
When addressing growing recipe complexity and higher levels of fat and protein, processors must consider a certain amount of flexibility in the equipment chosen to process these mixtures.
Wenger Manufacturing, Inc., Sabetha, Kan., develops cooking, forming and drying unit operations that cover a broad range of pet food applications, from plant-based and high-meat protein to the unique and nontraditional with engineered and often complex ingredients that often accompany the product.
“It’s about having a modular kitchen that can produce many different products while maximizing the operational efficiency,” explained Andy Hollister, product marketing director, companion animal and aqua feed divisions, Wenger. “This is the efficiency of having the right tool at your disposal and innovating by offering multiple options.”
The ongoing ability to accommodate unique and varied demands relies on finding the right partners to help determine the best equipment to meet a processor’s unique needs. Wenger advocates processors work directly with their equipment suppliers to determine the right tool.
“Processors should implement the correct, sustainable and flexible process, rather than trying to make equipment do what it can’t or should not do,” Hollister said. “We find many of our partners are limited by the processes by which they currently operate, and thus they are looking for value-added solutions that can add to the diversity of their products. When these partners come to us with limitations within their kitchen, we look to help them diversify – finding the right cooking device and tool for products now and in the future.”
With an ever-increasing number of customized formulas to run and an increase in the variables from recipe to recipe, consistency is a top focus.
“We’re observing a growing importance for precision process monitoring through the feed system – increasing consistency from batch to batch and shift to shift,” said Patrick McGady, Handtmann, Inc.
“The ability of equipment to replicate vacuum-filling processes and manage variables like temperature and pressure within tight parameters is very important, along with ease of maintenance,” said Patrick McGady, vice president sales and marketing, Handtmann, Inc., Lake Forest, Ill. “We’re observing a growing importance for precision process monitoring through the feed system – increasing consistency from batch to batch and shift to shift.”
Handtmann’s Vacuum Filler Cutting solutions possess the ability to run continuously for full shifts, and can quickly change extruded sizes and shapes while offering easy-to-use controls and simple extruder head swaps.
Others choose to look outside the industry for innovation, implementing equipment that has been readily available in human food production for years. Processors ready to look beyond rotary moulders, a longtime standard for kibble manufacturing, can explore using wirecuts to achieve the in-demand artisan appearance on a larger scale, Pallottini suggested.
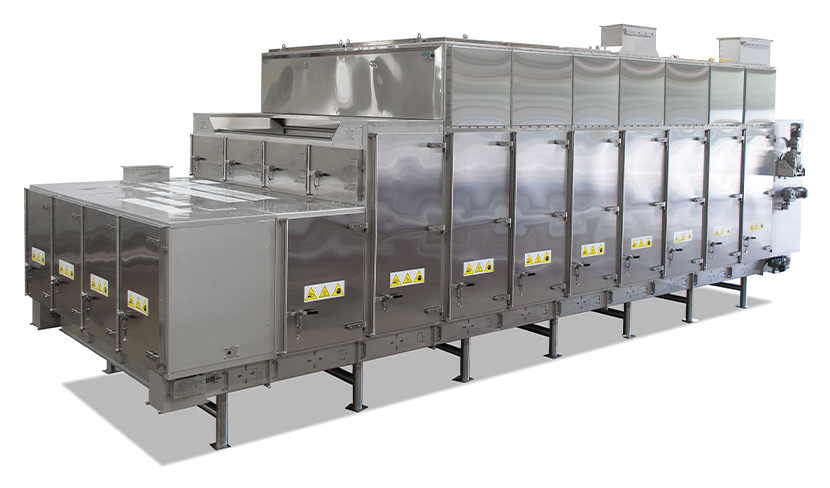
Just starting to reach the world of pet food and treats, wirecuts produce an artisan appearance by creating a rough surface while the feed rolls gently push the dough through a die. Reading Bakery Systems is also working on a low-pressure extruder to provide throughput and appearance to baked kibble and to increase the level of meat in the formulation.
With close to 400 million pets living in the United States today, pet food processors certainly have their work cut out for them. To serve this incredibly demanding and evolving demographic, processors must be on the lookout for ways to produce kibble accurately and efficiently using equipment that offers reliability and control to obtain the best profit margin and confident approval from the end user, Zeak said.
Those looking to keep pace with evolving human and pet food trends will find an ongoing advantage in working with trusted and established suppliers to improve existing products and boost plant efficiencies, helping processors make the most of available technologies while optimizing data collection and analysis to become more sustainable.
“Commission machinery that best suits your needs with opportunities for expansion that can meet your future needs, and work with an established supplier that provides skilled service and support around the world and who seeks to standardize materials and provide a quality process with checks in place that strive for cleanliness and consistency,” Carney concluded.
Find more articles about the latest pet food processing technologies on our Equipment page.