This article was published in the March 2024 issue of Pet Food Processing. Read it and other articles from this issue in our March digital edition.
The saying “work smarter, not harder” is thought to originate back to the 1930s when industrial engineer Allen F. Morgenstern coined the phrase while developing the first work simplification program. The purpose of his program was to increase people’s ability to produce more with less effort. That work philosophy has guided production processes for decades and helped bring about the evolution of manufacturing automation.
The designers and builders of Hill’s Pet Nutrition’s new “smart” facility in Tonganoxie, Kan., took that philosophy to heart as they integrated innovation, automation, sophistication and optimization into the 365,000-square-foot greenfield wet pet food production plant. This latest addition to Hill’s manufacturing sites started production October 2023, with goals of doubling the company’s wet pet food capacity once it’s fully commissioned in Q2 2024.
“The technology and advancements of this facility set it apart as one of the high-water marks in the pet food industry,” said Chad Sharp, director of manufacturing for Hill’s Tonganoxie.
The more than $450 million investment by parent company Colgate-Palmolive Co. showcases its mission to move toward more smart factories throughout its corporate network.
“Hill’s is a vital part of the Colgate-Palmolive company and our investment in this impressive new plant represents our commitment to Kansas, the growth of our business, and the advancement to our purpose,” said Noel Wallace of Colgate-Palmolive.
“Hill’s is a vital part of the Colgate-Palmolive company and our investment in this impressive new plant represents our commitment to Kansas, the growth of our business, and the advancement to our purpose,” said Noel Wallace, chairman, president and chief executive officer of Colgate-Palmolive, at the Oct. 16 facility grand opening. “By investing in this plant, Colgate is investing in growth. The sophistication and precision of the Tonganoxie plant will lead to greater innovation in our product formulation and will marry our industry-leading science with our unrivalled team and the best manufacturing technology, which is an unbeatable combination.”
Kansas is not only home to the new wet pet food plant, but also to Hill’s global and US headquarters in Overland Park, its Pet Nutrition Center and Small Paws Innovation Center in Topeka, and two other manufacturing facilities in Topeka and Emporia.
Governor Laura Kelly has long supported Hill’s investment in the state, as she iterated during the grand opening event.
“I could not be more pleased that Hill’s is increasing its investment in our state by opening this facility,” she said. “This significant investment is creating more than 100 good-paying, skilled jobs for Kansans. And importantly, this facility shows that Kansas businesses are moving forward. They’re not just keeping up with the economy, they’re also incorporating the technology that ensures they are setting the standard for manufacturing in the 21st century.”
|
Smart partner
The early stages of planning for the new Tonganoxie facility started in the summer of 2020 when the company realized there was a growing need for more wet pet food production, and its existing plants were not going to be able to satisfy continued growth in the long term. By the end of 2020, the company had committed to the greenfield project and in early 2021 planning began.
It was at this time that Hill’s chose Gray as its project partner. The Lexington, Ky.-based fully integrated service company provided engineering, design, construction, digital and equipment manufacturing services through its Gray family of companies, including Gray Construction, Gray AE, Gray Solutions, InLine Engineers, AD Process Equipment and Anderson Dahlen companies.
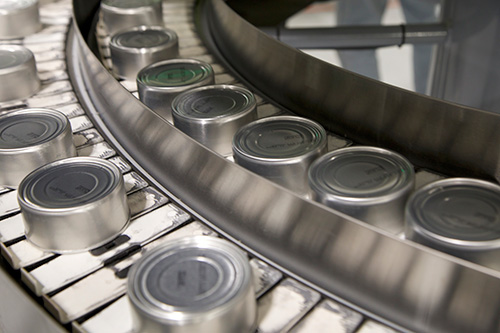
Hill’s new plant will ultimately double the company’s wet pet food capacity.
|“Gray was the design/build lead for everything you see here today,” Sharp said during the October grand opening. “They helped prepare all the raw materials, equipment and services needed to make this site a reality. Gray has built one of the most impressive manufacturing facilities we’ve seen.”
Hill’s worked in close partnership with the Kansas Department of Commerce, the Leavenworth County Development Corporation and the city of Tonganoxie to choose its site location. The access to a diverse pool of workers, a welcoming community, and proximity to distributors and suppliers all played into the company’s decision to choose the 80-acre plot in Tonganoxie.
“We’ve really tried to partner with the community… to give back where we can,” Sharp said. “We want to be good partners to the community of Tonganoxie.”
Part of that partnership involves working with the Tonganoxie Recreation Commission to help build the community’s first dog park.
Throughout the project, Gray lent its expertise in automation, sanitary process, engineering and advanced controls. More specifically, the project included property acquisition and permitting, civil, structural and architectural engineering, procurement and construction. The company also provided insight on the integration of automation and robotics throughout the plant, from ingredient handling to packaging.
“From advanced robotics to fully integrated process systems, every part of this facility is optimized to increase output and efficiency,” said Ben Bowzer, project executive for Gray.
After construction was complete, Gray continued to work with Hill’s on installing, programming and commissioning the equipment throughout the facility, and will continue to provide ongoing operations support as the plant ramps up production.
“The relentless effort of the teams is what made this project possible,” Bowzer said. “From the very beginning, Hill’s and Gray have worked hand-in-hand through the complexities of this highly technical, ultramodern facility that will now have an impact on this region and the industry for decades to come.”
Above and beyond
The immensity of the construction project and the state-of-the-art facility that resulted is hard to project even with the statistics Sharp shared during the grand opening:
- 650,000 cubic yards of earth were moved;
- 5,500 tons of steel;
- 25,000 cubic yards of concrete;
- 1,500,000 linear feet (almost 300 miles) of electrical wire;
- 365,000 gallons of storm water capacity.
“Tonganoxie is the first designed-from-the-ground-up, fully ‘smart’ factory in the CP (Colgate-Palmolive) world,” Wallace said at the grand opening. “It takes the best of proven technologies for manufacturing sites and adds state-of-the-art innovations across the footprint. The technology in this plant is amazing with how we move materials across the facility to automated digital product quality assessments.”
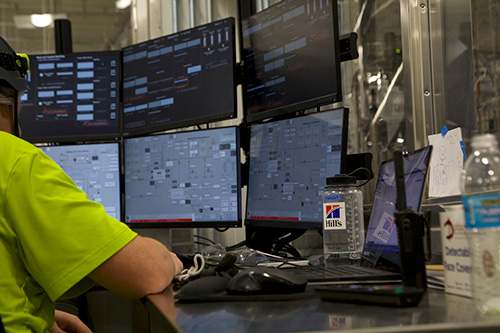
At the center of the facility is the plant’s Mission Control, which acts as a command center to track processes throughout the facility including ingredient dosing, product cooking and packaging.
|While automation, robotics and other smart technologies are starting to be added into other manufacturing operations in the industry as enhancements, the Hill’s plant was strategically designed from the ground up to incorporate these technologies.
“The Tonganoxie facility is a smart factory in many ways. From expert automation solutions to sanitary processes, engineering and advanced controls, we are able to leverage many unique technologies and capabilities,” Sharp said. “We have integrated controls and robotics central to the ultramodern plant design, end-to-end solutions for all of the process engineering, and highly automated process and packing equipment throughout the facility.”
All the smart technologies were part of the initial project design and supported Colgate-Palmolive’s corporate mission.
“Our company, Colgate-Palmolive, is working to embrace the smart factory side of things, every site is trying to be proactive where they can to enhance that,” Sharp said. “We saw this as a perfect opportunity to design all of that into our new location.
“We, as a company, want to lead on the technology so that we can improve things in our operations. Whether it’s speed to market, reliability or quality — all those things come into why we want to use technology in our facilities.”
The new technology and processes at Tonganoxie will help improve time to market by speeding up the production cycle for Hill’s wet products. The facility will manufacture all varieties of canned Science Diet and Prescription Diet formulas for cats and dogs. Separate processing lines produce the smaller 5-oz cans and larger 12.8- to 13-oz cans. Formats in the current portfolio include loaf, pate and stew products.
“This greenfield plant will not only help us increase our capacity and meet our demand, it will also allow us to unlock the power of cutting-edge science to improve the lives of pets with the development and manufacture of new nutritional solutions and product formats that best serve the needs of pets and the people who care for them,” said John Hazlin, president and CEO of Hill’s Pet Nutrition, at the Oct. 16 grand opening.
Included among the varieties of wet pet food produced at Tonganoxie will be its signature Hill’s Prescription Diet k/d, designed for the nutritional management of renal (kidney) conditions. The formulation was recently upgraded with a new proprietary microbiome technology that helps reduce harmful waste products.
“We’re proud that a new, upgraded version of k/d leveraging our advanced microbiome technology will be produced right here in Tonganoxie,” said John Hazlin of Hill’s Pet Nutrition.
“We’re proud that a new, upgraded version of k/d leveraging our advanced microbiome technology will be produced right here in Tonganoxie,” Hazlin said.
As more formulations are developed in the future and production increases, the plant offers room for expansion — both inside the current walls, and outside on the 80-acre site. Two additional processing and packaging lines could be added to the current floorplan without moving any equipment around or pushing beyond the existing walls.
“This facility was built for capacity and contingency,” Sharp said. “Capacity is necessary because we’re growing, and we need to keep up with that growth. The contingency means understanding our current network and being able to make sure we can always service the businesses and consumers the way they want.”
Front and center
At the heart of processing operations at Tonganoxie is the plant’s Mission Control room — located strategically at the center of the plant. Filled with computer monitoring stations linked to every part of the facility’s operations, the room acts as a command center to allow operations employees to track ingredient dosing, product mixing, canned product cooking and sterilization, packaging and distribution.
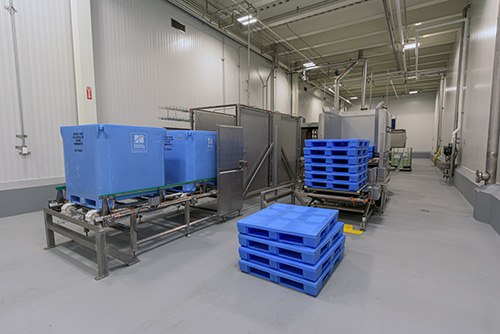
Ingredient totes and pallets throughout the plant contain RFID chips to provide autonomous robots with information on what’s inside and where the totes should be transported.
| Source: Ryan Alcantara Photography“Those working in Mission Control focus on all areas of the facility,” Sharp explained. “Our state-of-the art Mission Control Center provides unprecedented visibility and monitoring through every aspect of pet food making, from ingredient intake, dosing and batching and utility usage, all the way through final packaging.”
Because of its importance to all processes in the plant, Mission Control was “intentionally set to be the center of the facility,” Sharp added.
Employees throughout the facility are also equipped with tablets to help monitor controls around the plant floor.
In-plant efficiencies
Production is currently running 24 hours a day, five days a week with approximately 20 employees working on the production floor per shift. An additional 40 personnel hold support, management and office roles to make up the 100 new jobs the Tonganoxie plant provided the community after it opened.
While no manufacturing operation is functional and successful without the people who run the plant, robotics and automation are also crucial for operational effectiveness and efficiency at Tonganoxie.
“From advanced robotics to fully integrated process systems, every part of this facility is optimized to increase output and efficiency,” Sharp said.
The new plant is equipped with autonomous mobile robots (AMRs) and automated guided vehicles (AGVs) to help improve manufacturing efficiency and to alleviate some of the manual tasks usually performed by employees, such as transferring meats and other raw materials around the plant. The 600 pallets of meat used in the plant would normally be moved around with employee-run forklifts. Instead, AMRs take the ingredients where they need to go with the help of RFID chips located in the ingredient totes and pallets.
“The automation innovations permit Hill’s to refocus employee assignments on value-added tasks and more meaningful work while AMRs literally supply the ‘heavy lifting’ to safely move ingredients and materials around the facility,” Sharp said. “Using automation helps us to be more effective as humans.
“We don’t want automation to be looked at in a negative light — it’s a positive in our plant,” he added. “We are adding automation to enhance our team members’ abilities throughout their day.”
Charging stations are located throughout the plant so AMRs and AGVs are ready and available in different regions of the facility — another design for enhanced efficiency.
Processing automation also provides opportunities for product inspection and verification throughout the manufacturing process. Vision system technology helps with product inspections at various points of production.
“The facility allows for multiple places of verification to ensure our products are meeting the internal and external quality standards and protocols. These digitally enhanced inspections operate alongside our expert quality control staff,” Sharp said.
“We have done a lot around verifications,” he added. “When you dose ingredients, you want to verify that you have dosed correctly. We want to make sure we are providing the right materials at the right quantity. Doing that through batch verification processes is essential.”
As product flows throughout the plant — from ingredient receiving (meats, grains and liquids) to ingredient dosing to mixing and processing, then filling, sterilization and finally to packaging — the production process is a unique “enclosed system.”
“Our system is designed to prevent food exposure to environmental contaminants,” Sharp said. “The opportunity for potential contamination happens when you have open processes and we tried to limit that to the best of our ability.”
First, all ingredients are received indoors. Receiving bays were designed in such a manner that trucks can fully enter the bays and transfer materials without outside exposure. Depending on the ingredient — meat, liquids, dry grains or micro-ingredients — the components move on to their respective storage and distribution areas throughout the plant.
From this point on, ingredients are enclosed in bins, totes and silos and are moved to processing without open exposure to potential contaminants in the plant.
“You can’t see the ingredients moving from one stage to the other — the setup is very clean,” Sharp said. “We have designed everything to be as enclosed as possible — it’s crucial for food safety.”
Automation is also a crucial component on the packaging side of operations. After the cans are cooked and cooled, upside down, they are labeled, inspected and then flipped before palletizing. Two packaging lines separate the large and small cans which can pass through packaging at rates over 1,000 cans per minute.
Smaller cans are automatically double-stacked and organized 24 cans in a tray, while larger cans are packaged 12 in a tray. Trays are shrink wrapped and palletized with the aid of robotics, and shipped out of eight shipping bays daily.
Long-term responsibility
“As a state-of-the-art smart factory, Hill’s Tonganoxie will enable us to elevate our already industry-leading quality and safety standards. In addition, it will also demonstrate our commitment to sustainability and reducing our environmental impact,” Hazlin said.
The Tonganoxie facility was designed and constructed with sustainability in mind, addressing environmental concerns including carbon, energy, water, waste, transportation, materials, health and indoor environmental quality. Boasting all this, the plant has submitted for LEED (Leadership in Energy and Environmental Design) Gold certification.

Product is tested on every shift to ensure product quality and safety.
| Source: Ryan Alcantara Photography“Tonganoxie is designed to be kind to the planet and the people that work here… using less energy and water, fewer resources and generating less waste while creating a healthier work environment,” Wallace said.
The site also features a water reclamation system designed to harvest rainwater and wastewater to be recycled and repurposed for future on-site use. The system will greatly reduce overall water usage at the facility.
Additional recycling efforts will be spread throughout operations from ingredients to packaging materials, and the facility aims to be as close to paper-free as possible.
These sustainability efforts, alongside the automation and technological innovation that was built into the facility’s design, show Hill’s commitment to transform the way pet food manufacturing is done — working smarter, not harder.
“We had determination to create a new standard for the future of our organization,” Sharp said. “We found a way to develop a cultural foundation for what will live on past all of our time here in Tonganoxie.”
75 years strong
Hill’s Pet Nutrition celebrated its 75th anniversary with the opening of its state-of-the-art “smart” manufacturing facility in Tonganoxie, Kan. The plant, which features artificial intelligence, robotics and computer monitoring throughout the facility, is a far cry from the company’s roots in the kitchen of veterinarian Mark Morris Sr.
“For 75 years, Hill’s and our people have been working to transform the lives of pets through science-led nutrition,” said John Hazlin, president and chief executive officer of Hill’s Pet Nutrition, on the Oct. 16 grand opening of the Tonganoxie facility.
In 1939, a blind man named Morris Frank, co-founder of The Seeing Eye, approached veterinarian Mark Morris Sr. to help find better nutrition for his seeing eye dog Buddy, who was suffering from kidney failure. Dr. Morris tinkered around in his kitchen to develop the nutrition to address the canine’s renal disease, a formulation that would later become the No. 1 veterinarian-recommended pet food brand, Hill’s Prescription Diet k/d.
Science-led pet nutrition has been the company’s hallmark since its inception and has guided Hill’s through its evolution and notable milestones:
1939 – The first version of Hill’s Prescription Diet k/d is created.
1948 – Hill’s Pet Nutrition is officially in business.
1953 – Morris’ work on therapeutic pet nutrition leads to a breakthrough in urinary pet foods.
1968 – Hill’s Science Diet pet food is created.
1976 – Colgate-Palmolive purchases Hill’s Pet Nutrition.
1992 – Hill’s creates first thixotropic pet food.
2004 – Hill’s develops first pet nutrigenomics research lab.
2018 – Hill’s expands pet research to include the pet microbiome.
2023 – Hill’s opens new “smart” facility in Tonganoxie.
Get an inside look into Hill’s Pet Nutrition’s smart facility.