Fueled by an increase in pet ownership and evolving trends to focus more on pet health and food nutrition, the global pet food market is expected to expand at a CAGR of around 8.5% over the next five years. While being part of a growing industry is every manufacturer’s dream, growth comes with its fair share of challenges as capital expenditure is limited, labor in the sector is dwindling, and production facilities are often riddled with aging equipment and manual processes that challenge productivity.
To meet rising demand with limited resources, you must maximize the potential of your current equipment and processes. But how? The short answer – automation. Let’s explore how incorporating the right combination of automation tools, including in-line robotics, advanced vision systems, and state-of-the-art artificial intelligence (AI) algorithms, can enhance your current assets and processes, preparing your plant to take on future challenges.
Robo-Rescue: Bridging Labor Gaps
As many seasoned workers embark on retirement and Gen Z shows little desire to fulfill the hot, heavy, and hazardous jobs often found on factory floors, meeting the impending increases in demand can feel daunting. Rather than fiercely compete with other manufacturers for the limited available workforce or waste time hiring and training workers who quickly realize these jobs are not for them, tackle your labor shortage for good. It’s time to welcome the steel collar worker.
By bringing robotic forces to the floor, you can permanently fill those always open positions; automate mundane, repetitive, and unsafe tasks; focus your valuable human resources on more critical jobs; and take down many of the inefficiencies standing in the way of reaching peak production.
Incorporating Next-Level Quality Measures
Pets are a part of the family and owners want to be sure they provide the safest and most nutritious food possible. As a pet food processor, ensuring your products are safe is a huge responsibility. Stringent food safety regulations in many places align with human food safety standards, especially since pet food is often an item that is all too tempting for children to try.
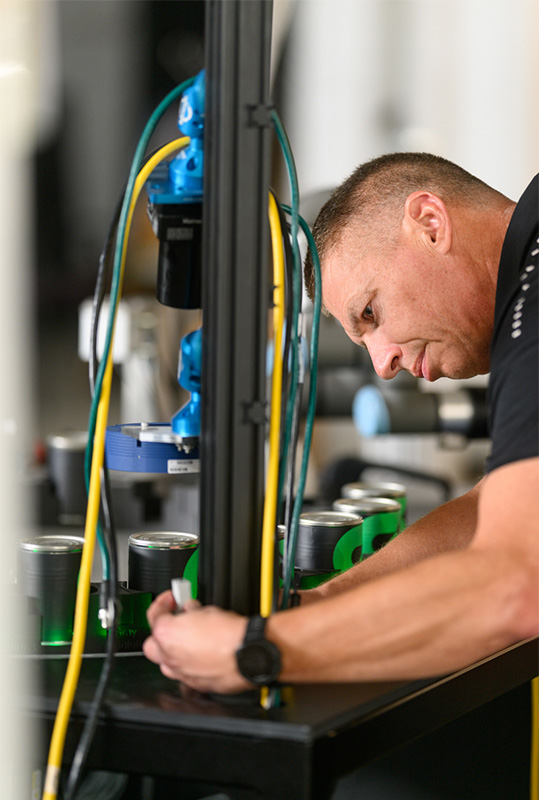
“When processes such as tracking raw ingredients or recipe management are manually performed, it’s incredibly easy for mistakes to be made,” says Diaz McDaniel, Senior Manager of Process Engineering at Gray Solutions. “Instead of passing paper around the plant or digging deep into spreadsheets to ensure recipes are precisely followed and products are closely tracked throughout the entire production process, a software-based track and trace system can be added to your existing equipment.”
With this digital toolset in place, everything from the raw materials going into the food to exactly where pallets of products are delivered is automatically tracked. This end-to-end transparency will help you better comply with regulations, and in the unfortunate event of a recall, greatly narrow the scope to specific batches, limiting both the physical and societal risks.
Another automated quality-boosting tool to consider is the addition of a clean-in-place (CIP) system. With a CIP, equipment cleaning between runs of different food blends is automated – reducing changeover time and ensuring cleaning is much more thorough than what a human is capable of, e.g. hotter water can be used when you don’t have to worry about scalding human hands. CIPs also help avoid issues like cross-contamination, which can be detrimental when you need to process food blends that guarantee certain allergens aren’t present.
Overcoming the many limitations of the human eye – from the speed at which we can read to the spectrum of colors we can see – with vision-based inspection systems incorporated throughout the production process can also greatly improve quality. Vision systems automate and greatly accelerate many mundane inspection-based quality tasks, from examining incoming raw materials to checking the containers food is packaged in for cracks or contaminants to ensuring products are perfectly packaged and palletized before heading out the door.
Let Curiosity Lead - Gray Solutions from Gray Solutions on Vimeo.
“The speed at which many of these tasks can be achieved is mind blowing,” says Adam Richards, Food Safety Engineer at Gray Solutions. “Just imagine the throughput increases you’ll see when a vision system is inspecting 1,200+ cans per minute for proper serialization, or the enhanced quality you’ll experience as a vision system detects moisture levels in bags of kibble, preventing issues such as mold growth.”
Additionally, when vision systems are tied into your process controller, defective products can automatically be rejected, and alarms can alert operators of potential larger problems. When issues are identified early, corrections can be made long before an imperfect or contaminated product reaches consumers.
Tech Tailwinds: Adding Advanced Automation Tools
If you’ve already started to bring automation to your production line using some of these robotic and vision-based tools but are still looking for ways to get more out of your existing processes and equipment, there are additional advanced automation tools to consider.
Advanced robots such as Spot® from Boston Dynamics can take many of the measures already discussed to new levels. Spot can supplement your workforce by performing mundane tasks such as routine fetching missions to retrieve bags of ingredients for in-lab quality analysis. Improve uptime with Spot patrolling the factory floor scanning for potential maintenance issues before they happen.
In addition to robotic tools such as Spot, autonomous mobile robots (AMRs) can be used to improve your intra-facility logistics. Taking the difficult job of moving large quantities of raw materials or 50lb bags of finished dog food out of the hands of humans and into the arms of AMRs can greatly improve the speed and accuracy of material handling. Plus, AMRs are incredibly flexible and can be easily changed to adapt to dynamic production environments.
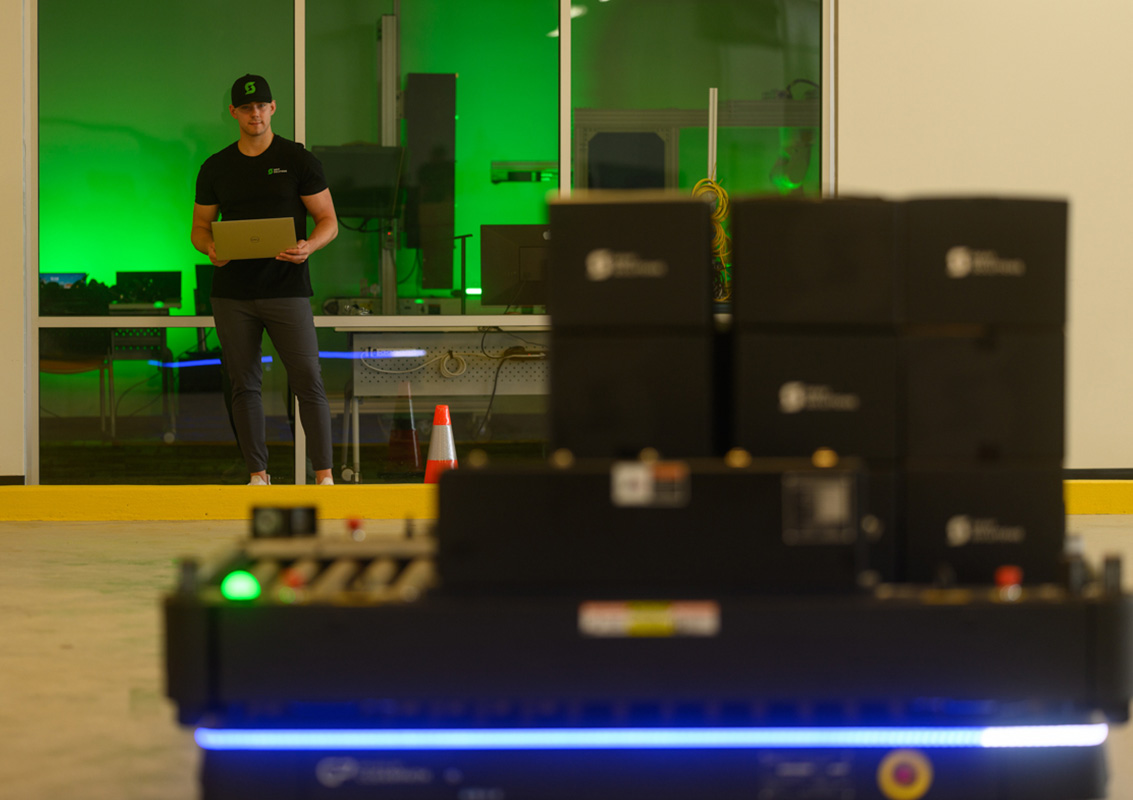
Finally, we must touch on the tremendous potential AI has to revolutionize many areas of the pet food production process. Machine learning algorithms can extract trends from data so you can fine tune processes for maximum efficiency or perform preventative maintenance before problems happen, alleviating emergency downtime. Advanced AI-based vision tools can boost quality measures as hyperspectral cameras for example can see color discrepancies the human eye could never detect, ensuring quality and optimum flavor by looking for incredibly subtle differences.
Embracing the Transformative Power of Automation
As the demand for pet food grows and pet owners place an increased emphasis on pet food quality, now is the perfect time to examine your current pet food production processes and identify opportunities to embrace automation and squander inefficiencies. But we know evaluating the many automation options available is overwhelming. So, let’s have a discussion. We can work together to create a plan to redefine what’s possible with your production by welcoming robotics to the plant floor and supercharging quality measures with advanced vision-based inspection systems.
Curious for more? Check out Pet Food Processing's article starting on page 24 of the March issue to see how Gray Solutions incorporated cutting-edge automation and robotics tools throughout Hill's Pet Nutrition’s new smart factory for wet food production, or visit www.graysolutions.com.