This article was published in Pet Food Processing’s 2021 Resource Guide. Read it and other articles from this issue in our Resource Guide digital edition.
Growth has been steady in the US pet food and treat industry, but it could have been even better for many if supply chain issues didn’t continue to challenge manufacturers. During Minneapolis-based General Mill’s first-quarter 2022 earnings call Sept. 22, Jeff Harmening, chairman and chief executive officer, said revenues were offset by higher-than-expected supply chain costs. At the beginning of the year, General Mills expected inflation of 7%.
“It’s clearly going to be between 7% and 8% now as we go on the year,” Harmening said.
Raw material vendors, internal manufacturing, co-packer manufacturing and its own distribution network all are impacting General Mills’ service levels, explained Jonathon Nudi, group president of North America Retail for General Mills.
“We have literally hundreds of disruptions in our supply chains, and it really changes on a daily and weekly basis,” said Jonathon Nudi, General Mills.
“It’s almost whack-a-mole right now,” he said. “So, we have literally hundreds of disruptions in our supply chains, and it really changes on a daily and weekly basis.”
Meetings at the senior level occur daily or weekly to solve the issues, he said. Additionally, industry-wide shortages in the labor market are impacting not only manufacturing facilities and distribution networks, but also raw material supply and external production capacity. To offset the impact of these challenges, General Mills is working with suppliers to extend lead times, use supplemental labor and encouraging more full pallet orders.
In its second-quarter 2021 earnings call Sept. 1, Chewy, Inc., Dania Beach, Fla., reported out of stock levels — although they were improving — remained elevated as a result of supply chain conditions in some areas such as wet dog food, which is being affected by industry-wide production capacity limitations. Mario Marte, chief financial officer, said supply chain and labor market challenges persist, and no one really knows how long or to what extent these might prevail.
Pet Food Institute (PFI) submitted public comments to the US Department of Agriculture (USDA) on June 21, detailing supply chain constraints seen by pet food and treat manufacturers, including those exacerbated by the COVID-19 pandemic. This was in response to the Feb. 24 White House Executive Order 14017: America’s Supply Chains, with the focus of better understanding and addressing supply chain issues seen throughout the US economy.
The association pointed to several issues in transportation and supply chain infrastructure, as well as how the interconnected nature of the pet food industry’s relationship to other US markets caused supply shortages and other disruptions in 2020 that have continued into 2021.
Ingredient and equipment challenges
Overall, ingredient costs have risen between 8% and 20%, with significant increases for corn and soybean ingredients used in most pet food formulas. Corn prices have risen 67% this year; and meat, poultry and fish ingredient prices are up 6.3%, according to PFI. These price hikes directly impact formulation costs for pet food.
These shortages and price increases are expected to continue through this year and possibly beyond. The USDA has forecasted an additional 1.5% to 2.5% increase in meat, poultry and fish prices through 2021.
Sources for animal- and plant-based fats and oils are also seeing “increasingly fierce competition,” PFI stated. Prices for these ingredients, as well as for palatants, have doubled as renewable fuel demand increases. Suppliers have responded by issuing “raw material product allocations,” meaning processors can only purchase a limited amount of each particular ingredient for their formulations.
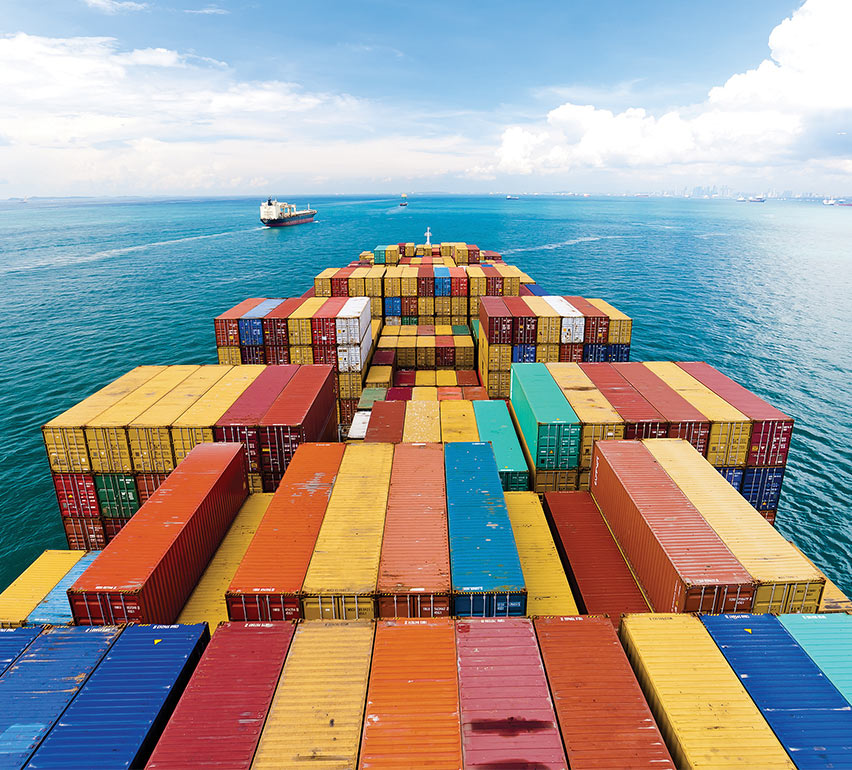
The association also shared lead times and pricing for major processing equipment have been “rising astronomically,” including manufacturing components such as valves, motors, pumps, coupling, stainless steel systems, piping and other equipment.
Transportation frustrations
“Systemic factors” have also contributed to distribution challenges for pet food and treat producers, PFI reported. While global exports totaled $1.7 billion last year and are expected to continue rising, domestic bottlenecks at US ports have interrupted the supply of certain imported ingredients — namely vitamins and minerals — to these manufacturers.
These bottlenecks have resulted in production scheduling challenges, higher costs and inefficiencies across the sector, and could hinder trade.
Driver shortages are also causing issues in distribution, with labor and turnover shortages reaching as high as 15% on a monthly basis, as reported by PFI members. Additionally, more than 10% of trucks are failing to show up to pet food plants on a daily basis, and a shortage of pallets is causing disruptions even if a driver and truck have already been secured.
Adapting as they go
Mitch Felderhoff, president of Muenster Milling Company, Muenster, Texas, reported supply chain challenges have been widespread and evolving with lead times changing constantly and product unexpectedly being unavailable. He said the predominant causes have been related to labor shortages from the supply chain or freight difficulties. To overcome these challenges, Muenster is producing product based on what ingredients are in stock rather than what is most efficient.
“We’re buying twice as much inventory as we were before, constantly interviewing additional supply chain opportunities, hiring additional staff any time we can and trying to be as transparent as possible with our customer base,” said Mitch Felderhoff, Muenster Milling Company.
“We have a constantly evolving production schedule which has forced us to build inventory aggressively so we can meet customer demand,” Felderhoff said. “We’re buying twice as much inventory as we were before, constantly interviewing additional supply chain opportunities, hiring additional staff any time we can and trying to be as transparent as possible with our customer base.”
Looking forward, Felderhoff expects anything affected by ocean freight will continue to be a struggle for 12 months or more due to container shortages, cargo freight shortages and COVID-19 challenges within the countries exporting supplies to the United States.
For NaturPak Pet, Janesville, Wis., lead times for supplies keep increasing due to the availability of raw materials, transportation — both domestically and internationally — and packaging.
“Over the course of the last 18 months, we have learned to plan our productions based off the new lead times, but it takes much longer to get from raw materials ordered to finished product,” said Kevin Carroll, key accounts manager for NaturPak Pet. “We have invested in equipment to increase our production allowing us to purchase larger quantities and be less dependent on transportation.” Based on communication from NaturPak’s suppliers, the company expects domestic and international transportation issues will continue.
Executives at General Mills also expect rising input costs, labor shortages and supply chain issues to persist.
For the foreseeable future, the supply chain environment will remain dynamic and challenging for pet food processors with supply and demand imbalances and constrained transportation and labor markets.
Read more about supply chain topics affecting the industry on our Operations page.