FRIEDRICHSDORF, GERMANY — Today’s conveying equipment must be multifaceted to keep up with the demands of modern pet food and treat processors. Not only must a product transfer solution get product from point A to point B, but it must do so in the most efficient, sustainable and safest way possible.
These systems come as an investment, making it crucial for manufacturers to understand what they’re buying before pulling out the company credit card. This is where OEM test facilities come into play, which offer processors the opportunity to try before they buy, often supported by the expertise of seasoned process engineers and salespeople who represent the supplier and its solutions.
Testing, testing…
According to Cablevey Conveyors, most processors inquire about equipment testing to examine product fragility and damage, quality assurance, reducing product loss and maintenance, and sanitation. Others are looking to compare various conveying options or discover how a tubular cable conveyor could benefit their business.
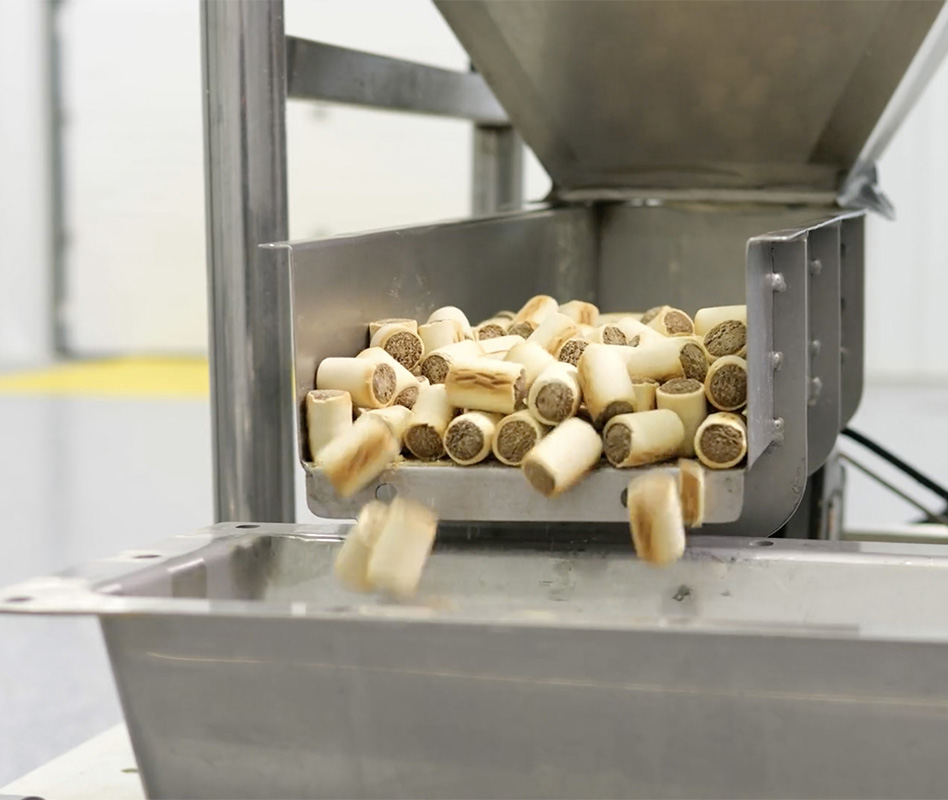
Pet food processors who “test drive” their product in this way will not only enhance their product quality and productivity, but also experience a significant advantage over competitors.
| Source: Cablevey ConveyorsAccording to Emmanual Ricohermoso III, Ph.D., testing and facility manager at Automated Handling Solutions (AHS) Germany GmbH, parent company of Cablevey, testing equipment before making a purchase is a progressive approach that can optimize design and material selection for durability, efficiency and environmental impact.
“From the client's perspective, conducting product testing offers them the valuable opportunity to experience the device firsthand before making a purchase commitment,” Ricohermoso added. “It allows them to assess the device’s performance, functionalities and suitability for their specific needs without the obligation of buying it outright. Additionally, during the testing phase, clients can engage directly with our knowledgeable team, leveraging their technical expertise to address any questions or concerns they may have.
“This interactive experience fosters better communication and understanding between our team and the clients,” he added. “Ultimately, seeing the device in action reinforces the clients’ belief and confidence in its capabilities, validating the effectiveness of the solution being offered, or simply, ‘to see is to believe.’”
The company’s 645-square-meter (6,942-square-foot) testing facility is centered around a test workshop equipped with product transfer systems from brands that fall under the AHS and Advanced Material Processing (AMP) umbrella, including Cablevey, Spiroflow, Kason and Marion. The test workshop itself accounts for 71% of the total space.
According to Ricohermoso, the German test facility was designed to not only enable testing of conveyors and material transfer systems from point A to point B, but to also integrate relevant processing steps including bag conditioning, bulk bag discharging and filling, dewatering, sieving, mixing and drying.
“Additionally, the test facility boasts a cutting-edge, in-house laboratory dedicated to material characterization,” he noted. “This enables our engineers to gain a deep understanding of the material properties, allowing them to design tailored solutions that meet the specific needs of our customers.”
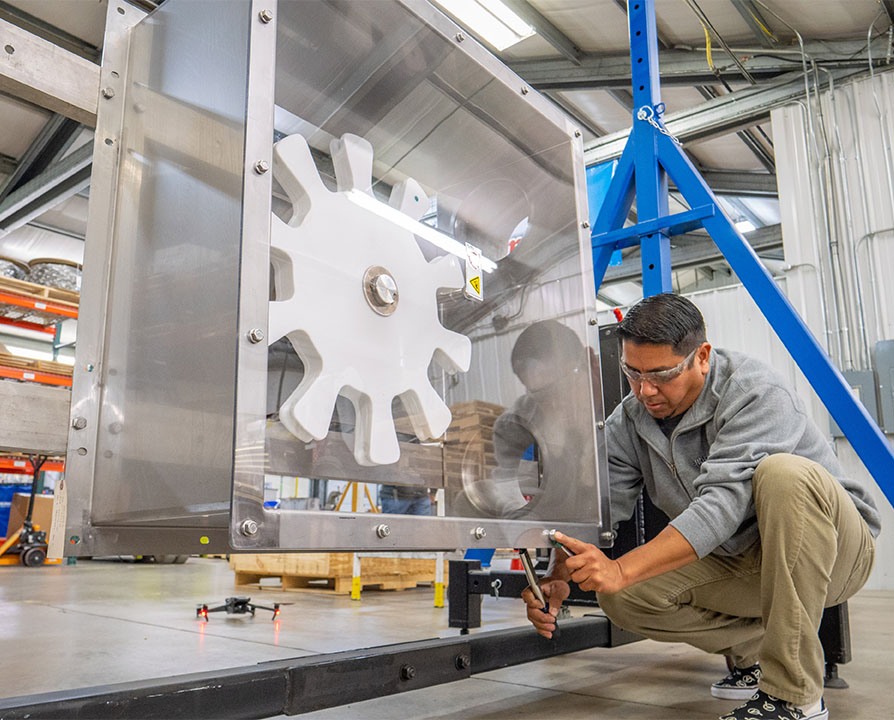
Technicians and engineers can diagnose and prescribe a solution whether the concern is breakage, temperature, stickiness, abrasiveness, or other issues.
| Source: Cablevey ConveyorsThe Friedrichsdorf test facility is now up and running and saw its first customer in early May 2023. Ben Ayrton, managing director and vice president of operations and supply chain for AHS and AMP in Europe, noted that the facility is now fully operational and offers more than 50 products for customer trials and testing across all four brands.
“We are immensely proud to have the most comprehensive testing facility in Continental Europe,” Ayrton said. “Our expansion and future is exciting, as in addition we are looking forward to introducing a brand new 5,500 m square production facility in the UK in the first half of 2024.”
The Friedrichsdorf facility will serve multiple AHS and AMP brands for testing, spare parts, European engineering and sales, as well as aftermarket spare parts and maintenance teams.
Prioritizing positive client experiences
Understanding why clients want to test or compare equipment performance is the No. 1 consideration when developing a test plan. For example, Ricohermoso said one of the main focuses for today’s pet food processors is throughput.
Once he has a better idea of a client’s priorities, Ricohermoso requests a Material Safety Data Sheet (MSDS) to better understand the handing requirements and potential risks related to the product or material in question. He also asks for cleaning, process flow integration, and tolerance information to create a comprehensive test plan for the client.
“If the client’s primary objective is to observe the operation without specific test requirements, I take the initiative to design the test plan myself,” Ricohermoso said. “The clients are then given time to review the plan internally and communicate any concerns they may have.
“By following this streamlined process, we ensure that the test day runs smoothly, with clear communication and alignment between our team and the clients.”
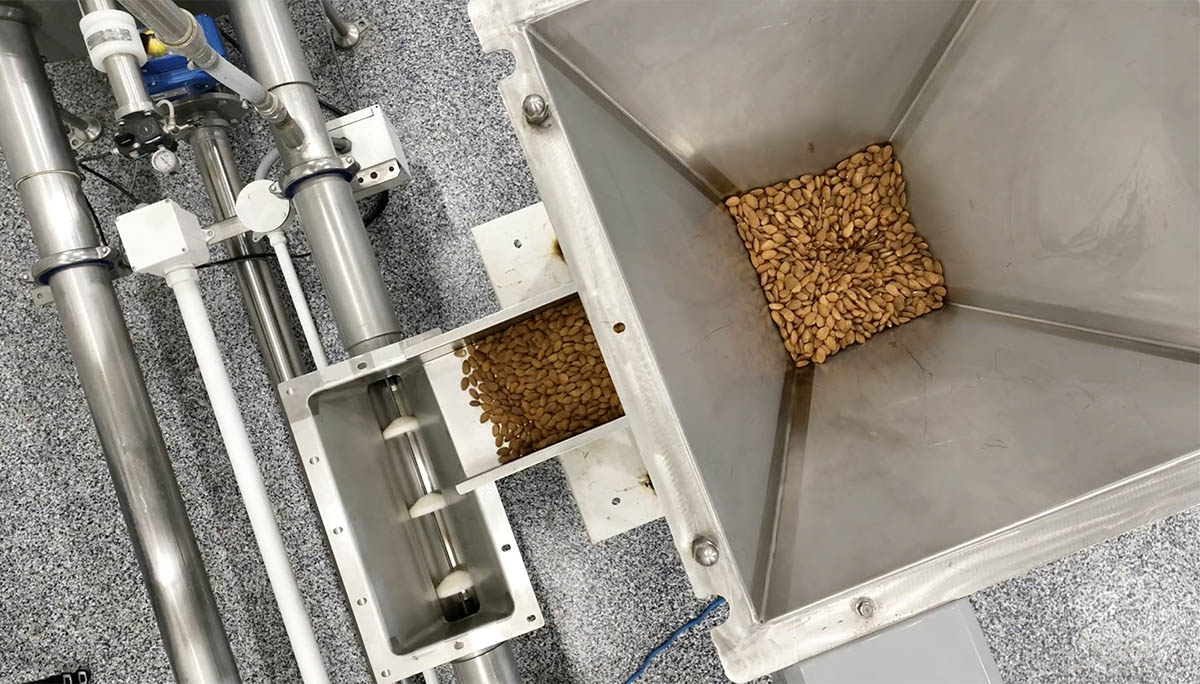
With easily accessible, advanced product testing facilities, pet food processors can view and verify in real-time that their investment in new conveying equipment will meet their requirements.
| Source: Cablevey ConveyorsLeaning on OEM expertise
Cablevey operates in more than 66 countries and has delivered its solutions for the food, pet food, coffee, powder, nut and frozen food industries for over 50 years. Such equipment includes enclosed cable and disc tube conveyors.
“Cablevey provides a gentle conveying solution, making it particularly suitable for products that are sensitive and have low tolerance for breakage,” Ricohermoso said. “Its unique conveying method ensures that fragile products can be transported without compromising their integrity or quality.”
At Cablevey’s stateside test facility — which is located in Oskaloosa, Iowa — the company recently launched a 360-degree immersive experience enabling virtual visits in real time. A Zoom-meeting format developed during the COVID-19 pandemic now allows Cablevey to showcase test runs of its machinery in-person and online simultaneously, which provides convenience for those unable to travel or larger work groups, according to the company.
Ricohermoso noted the company plans to add this capability to the German test facility over the next few months.
Find more articles related to pet food and supplier facilities.