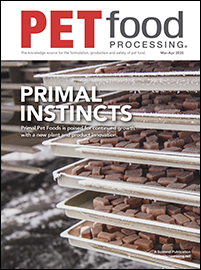
Not long after opening its new treat facility in Delano, Minn., Tuffy’s Treat Company put its flexibility to the test by adding a canning line to the plant.
Nearly 60 years ago, Darrell “Tuffy” Nelson started Tuffy’s Pet Foods with just 13 employees in the Perham, Minn. community. Today, the company has the capabilities to produce three core formats for the pet food market: kibble, dry treats and canned pet food.
Tuffy’s Treat Company broke ground on its 173,500-square-foot pet treat plant in Delano, Minn. almost three years ago and, since then, operations have been in full force. From ground-breaking to operation, the new $65 million pet treat plant was up and running in 14 months. The plant started running one shift, producing salable product, in October 2020. Three months later, a second 12-hour shift was added and by nine months after startup, three 8-hour shifts were operating.
Food safety standards were built into the facility from the beginning. When CRB took on the assignment of designing the greenfield facility, the company was tasked with building a plant that could maintain segregation, cleanability and sanitation without risking efficiency. A few of the plant’s quality and safety features include two dedicated ingredient receiving docks — one for wet, one for dry — to ensure ingredients remain separated until they’re added to formulations, as well as segmented pre- and post-kill areas to avoid cross contamination throughout the facility. All products go through rigorous testing to ensure quality and safety.
The plant was originally built to have room for four separate extrusion lines, but some of the space was taken in the short-term to incorporate the new canning line. Currently, there is one single-screw and one twin-screw extruder running pet treat products, usually for different companies, on a daily basis. Each line can produce 9,000 lbs of semi-moist pet treats each hour. After extrusion, grilling and cooling, the product is sent directly to packaging.
In order to stay flexible and allow for product runs of all sizes to go through the facility, Tuffy’s opted to incorporate six packaging positions into the new plant — three of which are designed for smaller batches and quick turnover. The company is currently running five of the lines and will soon add the sixth. The packaging distribution systems feeds, separates and weighs product before it is fed directly into pre-made, standup, resealable pouches or into one of two rollstock machines.
Packages are filled, weighed, inspected and put into cases before fulfillment. The packaging lines at the Delano plant were designed to blend both automation and flexibility, with hand-packed lines to allow for customization and flexibility, and automated lines for larger customers, driving labor efficiency.
While Tuffy’s pet treat production is running 24 hours a day on three shifts, the company is still growing and adding to the team, thanks to the addition of the new canning line that began production this February. Fifteen employees were hired to work on the current single shift of the canning operation. By the year’s end, Tuffy’s hopes to have an additional 30 employees running three shifts.
Canning is set up as a separate production and packaging line, with finished product stored at an off-site warehouse for fulfillment. All SKUs currently produced at the plant are Tuffy’s branded NutriSource products, in 5 ½-oz and 13-oz cans for dogs and cats.
Empty cans come in on a pallet and are lined up for inspection before any product is added. Before cans are filled, meat is ground and mixed with other dry and wet ingredients to form the pâté and then precooked. After the cans are filled, lids are placed and the cans are sent through a checkweigher, can washer, x-ray machine and then code dated before being layered into baskets for retort. While cook times vary depending on the moisture level of the product in the can, a typical cook and cool cycle in the retort/pressure cooker is around 1 ½ hours.
Tuffy’s long-term goal is to have the canning line outgrow the Delano facility in the next two to three years. When that time comes, Tuffy’s might opt to use the additional 20 acres it pre-purchased next door to the Delano plant, or it could build another plant elsewhere. For now, the plan is to add capacity and SKUs and to get more branded canned product on the shelves.
One of the primary missions of KLN Family Brands, parent company of Tuffy’s Treat Company, is “to make a difference in the lives of the people in our community region, state and country.” Whether in the town of Perham, Minn., the location of the corporate headquarters, or in Delano, Minn., home of the company’s newest manufacturing facility, the company is always on a mission to make a difference.
Take an inside look into Hill's Pet Nutrition's Tonganoxie facility.