This article was published in the March 2023 issue of Pet Food Processing. Read it and other articles from this issue in our March digital edition.
Companies that rely on reactive maintenance are waiting for a problem to happen, which can often be costly, leading to missed shipments, scrapped product, cost overruns, overtime and more.
“Unplanned downtime typically results in idle employees, loss in production, missed deadlines, and even long-term damage to brands,” said Caleb Otto, director of project engineering for NorthWind Technical Services, Sabetha, Kan. “Unexpected breakdowns can include costs such as overtime pay, contractor emergency fees, and overnight delivery of parts.”
Preventive maintenance programs, which have been the primary method to reduce unplanned downtime in the industry for decades, can help avoid these problems through long-term maintenance planning aided by real-time data.
Terri Ghio, president of Irvin, Calif.-based FactoryEye North America, noted that even something as simple as scheduled maintenance to clean, lubricate or replace parts that wear out can help keep equipment running longer.
“This schedule can be based on the calendar, the amount of run time, or even the amount of product produced,” she said. “For a lot of equipment, a more sophisticated form of preventive maintenance can be used that is based on the condition of the equipment.”
For example, in condition-based maintenance, significant leading indicators are monitored for changes so that the equipment can then have its preventive procedures performed prior to machine failure. This enables the equipment to run for as long as possible between scheduled maintenance tasks.
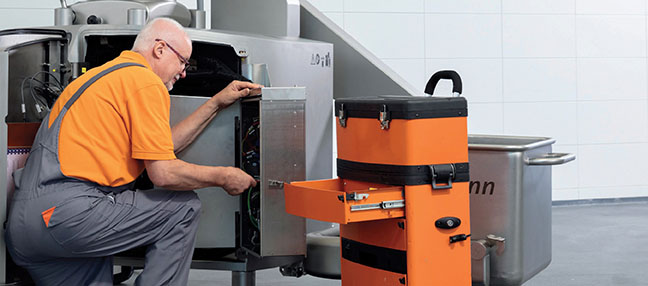
Preventive maintenance allows equipment suppliers to work with processors to catch potential issues before they occur, ultimately saving the company money. (Source: Handtmann Maschinenfabrik GmbH & Co. KG)
Fábio C. de Oliveira, an engineer on Wenger’s Brazilian service team, noted the company utilizes an extruder performance curve (performance x time) during a six-month window, and also considers working hours as additional data and the main product produced when designing a proper preventive maintenance program.
“Some customers work two or three work shifts and may need early preventive maintenance, and when this limit is exceeded, the extruder gives us signals when something is not working well,” he said. “Gradually, it will be possible to notice; oscillation of the extruder motor load, return of the product through the inlet barrel (product surging), difficulty for the operator to stabilize the process, and lack of uniformity in the product. The truth is that when it arrives at that point, the problem is already serious and increases the possibility of replacing a large volume of parts.”
Still, manufacturers can often be hesitant to implement new technology. This can stem from overall comfort level of embracing a new technology, willingness to deviate from standard department procedures, or the upfront cost of implementation.
Money matters
The cost to repair equipment can vary greatly depending on the type of machine and the type of maintenance being performed. However, preventive maintenance steps are almost always less expensive than a machine failure.
“As a typical example, a blown motor can cost tens of thousands of dollars to repair but keeping that motor in good condition through regular maintenance is usually inexpensive,” Ghio said. “It is akin to regular oil changes for your car or driving until the engine seizes up.”
“We catch things before they fail and save the customers money,” said Kelly J. Tebon, Handtmann.
When calculating the cost of equipment repairs, the cost of downtime cannot be excluded. A study by Aberdeen Strategy & Research estimates most manufactures will experience at least 800 hours of equipment downtime per year. That downtime comes at a cost. Hidden costs that are not typically calculated include supply chain responsiveness, reputation, and employee stress.
“The first step is to record downtime and the associated cost,” Otto said. “Once these metrics are collected, business decisions can be made to start reducing downtime with a strategy that works for you.”
It’s not just the cost of parts, but the fact that production capacity will decrease, de Oliveira said.
“For example, if an extruder in good condition that usually produces 10 tons per hour — consuming approximately 25 kw per ton — produces 7 tons per hour — consuming 32 kw per ton — it will spend more electricity, water and steam due to wear and difficulty in stabilization, ultimately producing less and decreasing the manufacturer’s profit,” he said.
Understanding challenges
Most maintenance management systems (MMS) include a way to define, schedule and track when preventive maintenance is required. However, these systems are often inaccessible to most of the people in the plant outside of the maintenance team.
“This can make it difficult for schedulers to know when the machines will be down or for production to incorporate that information into their plans,” Ghio said. “Also, a shift has been underway for many years to move as many preventative maintenance tasks to the operator as possible. This switch to autonomous maintenance can be difficult to support with an MMS. The operators need to know which tasks have to be performed on a given day and may need work instructions for the task if they are not the regular operator at that station.”
Tech evolution
Otto noted preventive maintenance technology has improved a great deal over the last five years. Just how far a processor takes its preventive maintenance program is up to each individual company.
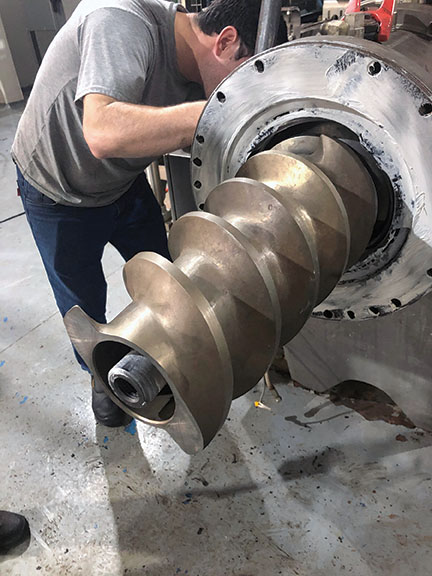
Wenger provides preventive maintenance service visits for its extruders to help customers solve potential problems before they occur. (Source: Wenger)
“Computerized maintenance management systems track schedules and send notifications for equipment maintenance,” he said. “Calculated equipment life expectancy and predictions for required maintenance can be calculated based on historical data. These software packages also help automate most of the administrative work.”
Beyond PC software packages, vibration, temperature, pressure, and other analog sensors are often used to detect worn equipment. This data, if used correctly, can detect an issue before the breakdown occurs.
What’s available?
Kelly J. Tebon, aftermarket business unit manager for Handtmann Inc., Lake Forest, Ill., shared that the company has been pushing preventive maintenance in recent years because several industry experts, who have hordes of knowledge on how to fix the equipment, are retiring and that knowledge is not being passed down to the younger employees.
“The whole concept is to bring us in on a preventive maintenance agreement, which gets us in periodically to do what we want customers to do, which is the 2,000-hour service,” he said. “We push our customers so they can get the lifespan they expect. We catch things before they fail and save the customers money.”
NorthWind provides maintenance management solutions as part of its overall suite of controls and automation offerings.
“It is akin to regular oil changes for your car or driving until the engine seizes up,” said Terri Ghio, FactoryEye North America.
“We implement maintenance tools and software packages to organize your maintenance team, utilizing historical and real time data to detect potential breakdowns before they cause downtime,” Otto said.
FactoryEye offers a modern solution that can fill the gaps that exist in legacy systems, based on the XPI integration platform by Magic Software, so it can easily connect to other systems in the plant and even to the sensors and machine controllers themselves.
“Because of this, it can track what is happening at the machine to provide condition-based alerts when maintenance needs to be performed,” Ghio said. “It can integrate with the MMS and to the machine, so it will know when scheduled tasks need to be performed and can make that highly visible within each user’s workflow who needs that information. Visual controls can be implemented at the machine to display autonomous maintenance task lists for the day and instructions when they are required.”
Wenger provides service visits for preventive maintenance on the extrusion line and also has its Wenger Care program for extruders and dryers, which includes options such as evaluation and process optimization, in addition to preventive care.
During the preventive maintenance, the Wenger team performs a quick inspection of the other devices that are around the extruder such as the downspout, live bin, feeder, agitator, level sensors, temperature sensors, BPV, head jacket and valves. The team also checks the steam and water injectors (eliminating possible obstructions), tests the devices starts, verifies that everything is working correctly, and, at the same time, collects information from the process team. The idea is to map and prepare for any eventual need that may arise.
“Through visual and dimensional evaluation of the extruder screws, sleeves and shearlocks, we can estimate their durability,” de Oliveira said. “The values found during inspection are registered, so the wear will be controlled over time, and we will know how much the parts have worn out and if it is possible to use it for another cycle repositioning them on the extruder shaft. By working in this way, we can extract the maximum durability of the parts.”
Time for something new
Many companies have a long list of preventive maintenance tasks for each piece of equipment. The list tends to grow over time as unplanned failures occur and tasks get added to prevent additional failure.
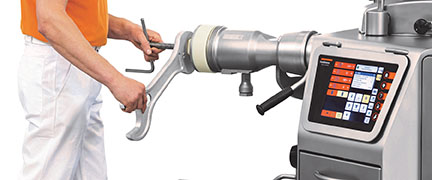
Pet food processors use preventive maintenance programs to help reduce unplanned downtime due to equipment failures. (Source: Handtmann Maschinenfabrik GmbH & Co. KG)
So, even with a great preventive maintenance program in place, eventually, equipment will need to be replaced. The most obvious sign of the need for new equipment is when excessive downtime starts to lead to problems in the plant.
Companies should ask themselves, “Are the failures still happening that the preventive maintenance tasks are supposed to prevent?” and “Are the tasks being performed more often than necessary?”
“If you cannot answer these basic questions, it is definitely time to take a look to see if there’s a better way,” Ghio said.
Find more articles about the latest pet food processing technologies on our Equipment page.