BOULDER, COLO. — The current recycling infrastructure for plastic materials is limited in the United States and Canada. This poses issues for CPG products like pet food and treats, traditionally sold in multi-laminate films that make recycling difficult, if not impossible. A sustainability surge is changing this, however, as more and more companies across this industry and others pledge to adopt more environmentally friendly packaging options now and in the future.
At the Pet Sustainability Coalition’s (PSC) UnPacked22 virtual packaging event in late February, three packaging specialists spoke about three different approaches: recyclable packaging, refillable packaging and compostable packaging.
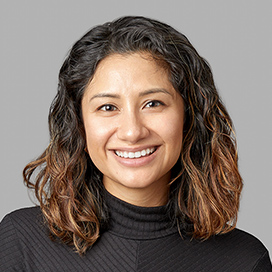
Paula Luu is the senior project director at the Center for the Circular Economy, an innovation center by Closed Loop Partners. The Center for the Circular Economy works with Fortune 100 companies to find circular solutions and alleviate supply chain bottlenecks for packaging materials. These priorities have been the focus of the Center’s research and development on molecular recycling over the last three years, Luu shared.
What is molecular recycling?
Molecular recycling is also known as chemical recycling or advanced recycling, Luu explained. The process uses various technologies to break down plastic waste into chemical products, according to Closed Loop Partners November 2021 report, “Transitioning to a Circular System for Plastics: Assessing Molecular Recycling Technologies in the United States and Canada.”
In explaining molecular recycling, Luu said, “It's not a monolith. It's really a diverse set of technologies that are leveraging either solvents or heat, or enzymes, even sound waves to purify and break down different types of plastic waste.
“There are three types of technologies within the sector: purification, which produce polymers; depolymerization, which produce monomers; and conversion technologies, which produce hydrocarbon products like naphtha, or diesel, or paraffin waxes,” she continued. “Each of these categories of technologies usually take in different kinds of inputs and are creating a diverse set of outputs.”
This advanced recycling approach is relatively new, compared to the more traditional mechanical recycling, but could play a significant role in improving plastic circularity in the United States and Canada, according to Closed Loop Partners’ research.
“When we began to investigate the gap between the supply and the demand for high-quality resins, what we found was that mechanical recycling alone is not likely to fill that gap,” Luu said. “The key difference between molecular recycling and mechanical recycling is that, because it is working at the molecular level, [molecular recycling] is thermodynamically resetting the power through various types of technology platforms, as we discussed, and it allows for the polymer to stay at its highest value. Said another way, it is only focusing on creating virgin-like polymers, and we can add different colors and additives to meet functional performance, and it is uniquely positioned to support mechanical recycling and join that gap between the demand and supply for high-quality resins.”
Thinking green
The firm’s research looked at the environmental impacts of molecular recycling compared to mechanical recycling, specifically in terms of energy use, water use and carbon dioxide emissions. Compared to virgin plastic systems, molecular recycling technologies generally consume less energy, emit less carbon dioxide, and use less water in their processes per plastic pellet produced. The report indicated using renewable energy could magnify these natural resource savings. The catch? Each molecular recycling technology creates a different kind of plastic resin from each other and from mechanical recycling streams.
"Pairing the two systems — mechanical and molecular recycling — is what's going to be the most strategic way to decarbonize our plastics economy," said Paula Luu, Closed Loop Partners.
“Pairing the two systems — mechanical and molecular recycling — is what's going to be the most strategic way to decarbonize our plastics economy, while also creating the supplies of recycled plastic that the market needs today,” Luu shared.
The financial side of the equation was also considered. Luu stated that, through Closed Loop Partners’ research, it was determined that there are investable, viable opportunities for each category of molecular recycling. High variability was observed for depolymerization, but 2021 market prices of polymers, monomers and hydrocarbon products created through molecular recycling technologies yielded strong ROI and expected IRR, according to the report.
“Understanding the ability for the sector to curate new commodity prices, based on the value proposition to a sustainable economy, is going to be really critical for its financial success in the market and for investors who are looking to scale these technologies,” she said.
A mixed approach
The onus of the research is developing a better understanding of our current recycling streams, plastic supply and demand, and how emerging recycling technologies like molecular recycling can improve on the package recycling rate across the United States and Canada. According to Closed Loop Partners, the current recycling rate of the two countries is 18%. Globally, the recycling rate is roughly 9%.
In order to reach a 30% recycling rate in the United States and Canada, advanced recycling methods must be scaled, invested in and innovated, and a combination of traditional and advanced technologies should be employed. This mixed technology approach — using mechanical recycling methods alongside purification, depolymerization and conversion solutions — is optimal from an environmental perspective and could double the amount of plastic packaging recycled today, generating up to $970 million annually, Luu stated.
“There's certainly a financial opportunity, there's an environmental opportunity on the table, and no one clear winner,” she said. “A mixed technology approach to deal with the variability of plastics and diversity of plastics in the system, as well as matching different technologies with different levels of infrastructure development across the market, is what's going to yield us the best results.”
It’s not all about downstream solutions either. While mechanical recycling and molecular recycling are downstream, end-of-life solutions to the plastic problem, brands can also make more sustainable packaging decisions upstream. This includes designing packaging materials differently and adopting non-traditional formats like reusable, refillable or compostable solutions.
“What brands can do from a packaging design standpoint is ensure that as much of their packaging is aligned to mechanical recycling, understanding that there are not always going to be the economic incentives to process all packaging through that system,” Luu said. “For our hardest-to-recycle plastics, including some packaging formats and especially outside-of-packaging formats, molecular recycling is a downstream option.
“…Acknowledging that investment is needed across the entire value chain, even downstream from the technologies to successfully integrate, is ultimately going to support the integration of these technologies and expedite commercialization,” she added.
Challenges and opportunities ahead
An important part of this process is getting consumers to place used plastic materials into recycling streams after use. Labeling plays a critical role here, Luu said, because it helps inform the consumer on which bin to place it in. However, this still doesn’t guarantee the item will ever be recycled.
“Infrastructure recovery systems are patchy, and that's true for molecular recycling, that's true for mechanical recycling,” Luu said. “…I think we're still many years out from that infrastructure really being fully commercialized, where something like ‘recyclable’ is a credible explanation of what's happening in the system.”
Large pet food bags are often made of mixed plastics, such as mixed PET-PE materials, or homopolymers with colors and other additives incorporated for functional use, which can pose issues for mechanical recycling. However, new advanced recycling methods can be used to break these mixed materials down, according to Luu.
Some new molecular recycling technologies Luu said she was looking forward to include purification technologies that can handle mixed plastic waste streams, as well as conversion technologies that use different platforms such as pyrolysis and gasification to achieve outputs of propylene or ethylene.
In fact, PSC’s Flex Forward pilot recycling program for used pet food and treat bags is currently exploring advanced recycling methods as a means to handle the more than 8,000 lbs of plastic packaging it collected in late 2020 and early 2021, according to Melissa Bauer, director of sustainability at PSC and co-host of UnPacked22.
Research and development will continue for molecular recycling technologies, and industry stakeholders advocating for a more sustainable sector, like the Pet Sustainability Coalition, will continue to push for the adoption of more circular packaging materials and improvements to recycling policy and infrastructure.
“Looking at policies like EPR [Extended Producer Responsibility] as maybe writing on the wall I think, irrespective of molecular recycling, our collections and sortation infrastructure is going to be changing and for the better,” Luu concluded.
“My biggest takeaway when I look at the financial, the environmental and human health impact work that we did over the last two years leading up to the latest report, is that the more that we invest in collecting and sorting our plastic, to direct them to the most mass-efficient and environmentally friendly kind of solution, the more all value chain stakeholders — be it the collections folks, the sortation folks, customers — have to win. Really, it comes down to our political will of investing into that upstream system.”
Read more about packaging solutions and trends for pet food and treats.